The Dwight D. Eisenhower Memorial, located on the south side of the National Mall in Washington, D.C., is a four-acre memorial park featuring a stainless steel tapestry, bronze sculptures, and stone bas-reliefs. Californian artist Tomas Osinski created the spectacular tapestry under the design of the world-renowned architect Frank Gehry. The Facade Screening System displays the Pointe du Hoc promontory of France’s Normandy coastline during peacetime. It serves “as a symbol of the peace Eisenhower won as Supreme Allied Commander during World War II.” The initial artwork was a photographic representation of the Normandy cliffs and French landscape compiled from images captured by a drone.
At 137 meters long and 18.5 meters tall, a Facade Screening System of this size is unique in its dimensions worldwide. Made of 604 panels, each measuring 1.2 meters by 4.5 meters, the tapestry is supported by a cable net system suspended from a stone-clad concrete colonnade of six columns, each standing 24.5 meters tall and 2.7 meters wide, spanning the Southern perimeter of the memorial. Pfeifer Structures designed, fabricated, and implemented the cable net system between 2017 and the opening ceremony on September 17th, 2020. We talked to Igor. G. Siotor, Enclos Tensile Structure’ Representative in Canada, about the specific circumstances, challenges, and difficulties of this groundbreaking project.
Mr. Siotor, first concrete ideas and planning schedules of the erection of an Eisenhower Memorial in Washington D. C. go back to the end of the nineties. After this, as we can see, there was a long and complicated history concerning the design process, especially the tender process of this specific project. But, most importantly for now, when did you get really involved in this?
It was at the end of 2014 when Frank Gehry started communicating with us. At this time, we as PFEIFER Structures had no idea what Gehry’s concept was all about; he did not even reveal the name or the location of the project. Instead, he asked for support about our technology, respectively the different alternatives in realizing a certain kind of lightweight construction.
So you started the project with no contracting, just supporting the design team of the Eisenhower Memorial Facade Screening System?
This is quite normal in our business, and for us it is a very good opportunity to contribute at an early stage of a project. This early support of design teams like we did for Gehry does not at all mean that we will be part of any later construction, in case the designer wins the competition. But it keeps us involved in the position of a technology leader in designing and engineering complex lightweight architecture all over the world.
But after Gehry had won the design competition, you were definitely in the project, weren’t you?
Not at all. In such a big and highly regarded project like the construction of the Eisenhower Memorial Facade Screening System, the process from initial support to final realization could be a very long and rocky one. The design team has neither the right nor the opportunity to select any engineering or construction company, only the owner – in this case, the Dwight D. Eisenhower Memorial Commission – may handle this. So the first step after approving the design was the selection of the general contractor. Five companies applied for this, and we were part of four of the five tenders. In the end, Clark Construction Group won the tender, and as a result of a further bidding process, we became their subcontractors for the design, fabrication, and installation of the cable net and tapestry.
Were you still in contact with Gehry’s design team?
Not only did we keep in contact, but we were collaborating very closely with Gehry because the realization of the Facade Screening System was strongly connected to the technical feasibility. The presentation of this piece of artwork stands or fails with the engineering and fabrication of the cable net. This project is not an ordinary or even special building: it is a piece of artwork, so we had to handle it as such. Therefore, it requires a totally different approach to construction. The overall appearance of the tapestry is all that counts. Our goal was for the structural support of the artwork to be as concealed as possible. Imagine a wall in a museum. You do not want to have anything there, just the plain white wall so that the visitor can focus on the artwork without any visual obstructions of the background.
In which way did this influence your design work?
It changes nearly everything. If the objective is that the supporting structure should be as small and concealed as possible, you still have to guarantee a normal level of safety at the same time. Keep in mind we had more than 600 panels, creating the image on the tapestry, each one 1.2 meter by 4.5 meter, which means 2500 square meters of a painting on a neutral wall. Our task was to construct and connect this all with a maximum of stability and robustness.
How did you manage the safety requirements?
Any structure has to be safe and conform to all codes and regulations one hundred percent. You can compare what we did in supporting the tapestry with the design of a bridge. You have different forces, which you have to consider in your calculations to build a long-time standing structure, like wind forces, snow, vandalism, freezing rain, as well as the weight and deformation of the construction. Finally, Facade Screening System and its support had to withstand an airplane propeller’s pressure and lose only six of the six thousand welds that were subject to simulated hurricane wind forces for one month. We conducted this test and other tests on a performance mock-up built prior to the start of actual construction on site.
What made this project special in the fabrication process?
For ETS, each project is unique. We rely on our engineers’ long-term experience and expertise, who are real experts in our technology. Even in this special context Eisenhower Memorial was “extra-unique”. This project was all about details. For example, we had more than 12,500 connection parts custom-designed by our Chief Engineer, Thomas Rieder, and specially fabricated for this project. We had to be very clear about that in the tender phase, so our pricing was realistic and competitive at the same time.
When did you start to fabricate the individual parts of the structure holding the tapestry?
After nearly a two-year phase of designing, planning, and the approval of our shop drawings, we started the fabrication in January 2019. The design and engineering process did not stop right away because some of the design requirements changed in the meantime. There was still a constant line of re-design and re-engineering work when production had already started. In fact, we needed around half a year to produce all the necessary parts for the cable net and all details.
When did construction start, and what was the main challenge to building this artwork tapestry on-site?
Together with our partners, we started construction in October 2019. After the engineering and fabrication, the installation of thousands of parts was a further challenge, mainly because the installation sequence had to be executed very carefully and precisely. The complex cable net structure, featuring a multitude of intricate connection parts, was constructed under a live load. Erection engineering is another part of ETS’s expertise. Performing all of these parts on one project by one company is the best example of our qualifications in the world of lightweight architecture. Another important issue regarding the construction was the timely delivery of the parts, which required coordination with the work schedule of other trades on site.
If you look back on the whole project: What is your final summary?
It is very simple: Frank Gehry and Tomas Osinski stated that they are happy with the final product and with ETSs’ performance. If they are happy, that means we have done our job well. In summary, I can say that at all stages of this challenging project, our company knew what to do and how to deliver the consultant’s design concept, from early sketches to the opening ceremony of the Memorial in Washington D.C. We accomplished this despite delays, changes and other usual issues on a typical construction site.
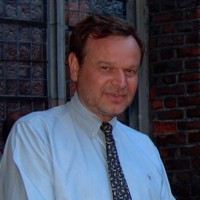
About the Author – Igor Siotor
Igor Siotor has worked with Pfeifer for the last 15 years as an industry leader in lightweight structures including structural cables wire ropes and tension rod systems. Prior to working with Pfeifer, Igor was a successful architect and a consultant to the tension membrane industry. Igor has been at the forefront of the innovation of cable structures and is a global leader in designing cable supports for bridge structures like the Beatus Rhenanus Bridge. Igor has published a multitude of papers and has been a featured speaker at various industry conferences such as the International Association of Shell & Spatial Structures.
Connect with Igor on LinkedIn: https://www.linkedin.com/in/igor-g-siotor-117a48209/